Small Industrial Premise Fit-out: Surpassing Energy Efficiency Goals
- Ir. Khim Bok Tan
- Mar 24, 2022
- 2 min read

The Brief
This client, Tonasco, is a mechatronics contract manufacturer focusing on single piece and low volume series production of high-tech mechatronic components, modules and complete machine.
In May 2013, this client commissioned IEN Consultants to provide Energy Efficiency consultancy for the retrofit of their soon to be new office at Bukit Jelutong, Shah Alam.
The brief was simple: They would be moving their current operations (Office & Production) to a new premise which would be 30% larger (by Gross Floor Area) but would like to keep the energy bills the same or lower than the current energy bill
Our Approach
We started off by understanding the client's current operations, building services design and analyzing the historical energy usage. The former was done through a visual site audit of the existing premise, while the latter was through compiling historical electricity bills. The site audit provided us with early ideas on where there could be potential for cutting energy usage. With the historical energy bills, we were able to set a benchmark for the energy usage intensity for the new facility.
We then reviewed the proposed fit-out design of the new facility and had discussions with the client on any operational criteria (e.g. space temperature and humidity, lighting levels, exhaust for equipment etc) for each of the different zones and functional spaces.
We carried out dynamic energy simulations using IES VE to not only estimate the potential energy savings of various ECM (Energy Conservation Measures) but also used this to verify the capacity selection of the proposed air conditioning units.
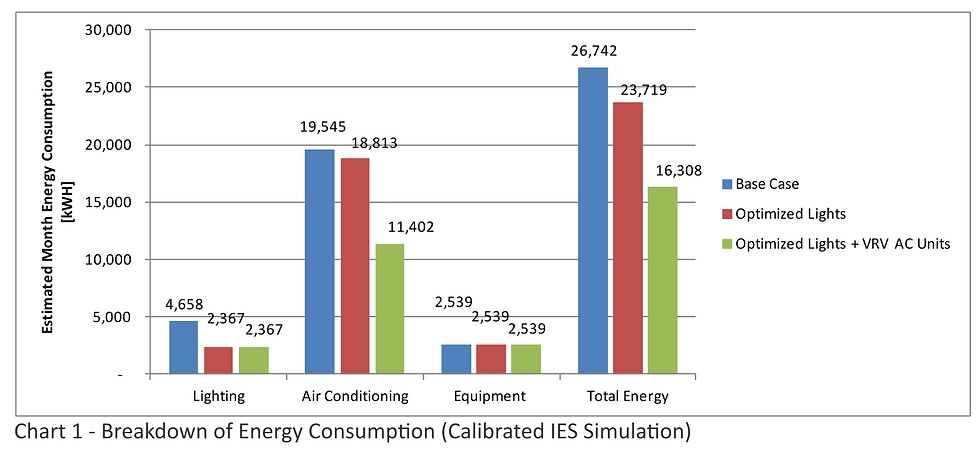
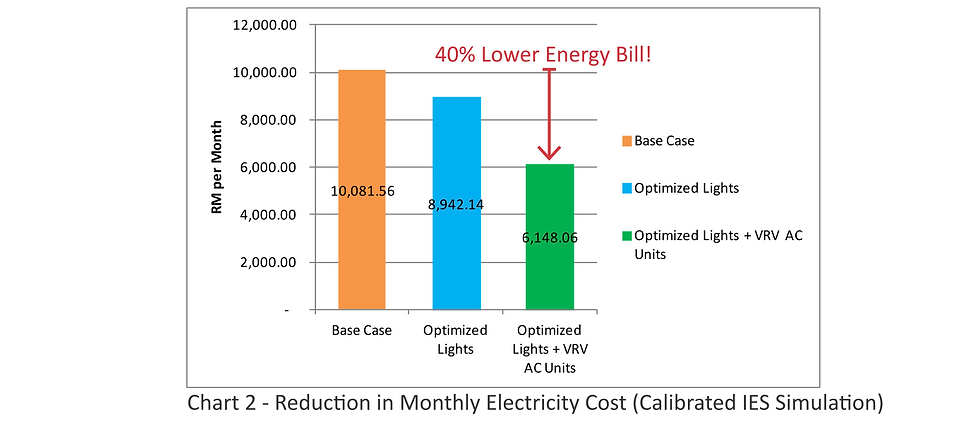
We also carried out daylighting simulations using Radiance for IES and electric lighting lux level simulations using DIALux to show possibilities to reduce lighting energy.

Our Recommendations
To meet the client’s requirement, IEN proposed the following Energy Efficiency strategies:
1. Electric lighting design would be optimized to ensure that only working zones requiring higher illumination would be brighter lit. Circulation spaces would not need to be as bright.
2. Existing dark tint of the external glazing should be removed to allow better daylight penetration and improved view-out.
3. Air conditioning system would be optimized both in terms of capacity selection as well as overall efficiency. VRF (Variable Refrigerant Flow) systems was recommended and was shown to achieve a payback on the additional capital investment within 5years. This payback period was achieved by ensuring there was little “over-sizing” of AC capacity and equipment with high COP (average COP 3.8) would be selected
The Outcome
After 5 months of operation, the following are the recorded energy consumption and electricity cost (Source: TNB bills)


With the few simple but effective energy efficiency strategies implemented, the client was able to reduce their energy consumption and electricity bill by 40% (approximately RM4,000/month or RM48,000 per annum) compared to a Business-As-Usual (BAU) scenario. Even more interestingly, the average BEI (Building Energy Intensity) was reduced 350kWH/m2*year at the old premise to 190kWH/m2*year at the new building. That’s a staggering 45% reduction!
Based on the additional capital outlay (primarily on the upgrading of the AC system), the savings in electricity would result in a payback period on investment of approximately 5 years.
Comments